Have you ever noticed the smooth and glossy surface finish on products made using investment casting? It’s a sign that even the most intricate pieces can be created with precision and accuracy. But how is this achievable?
In this blog, we’ll delve into the world of investment casting to uncover the secrets of achieving a perfect surface finish. So, if you’re ready to take your product designs to the next level, let’s get started!
Benefits of Investment Casting
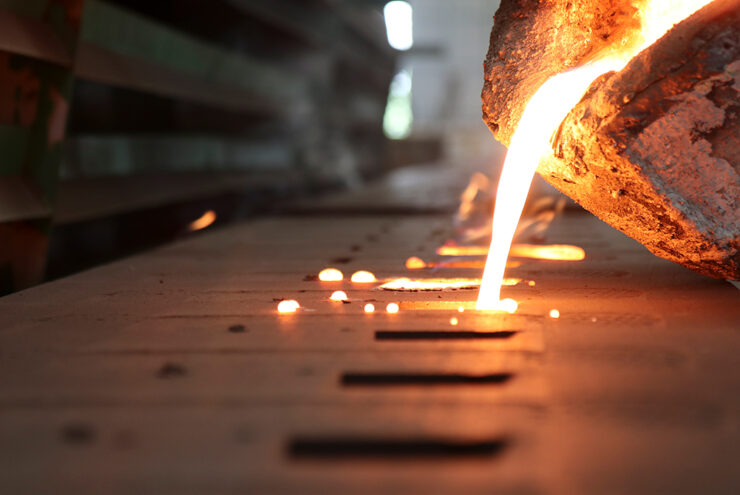
Investment casting offers several distinct advantages over other casting processes. It generally produces more detailed and complex parts using simpler and fewer tools, as well as shorter lead times.
Also, because the molds are produced using a ceramic shell, the walls of an investment-cast part can be made thinner than any other manufacturing process. This helps to produce a lighter component too, which can mean cost savings in other secondary operations such as machining, finishing and assembly.
Additionally, since there is minimal machining requirement for investment castings, surface finish can be improved.
Factors Affecting Surface Finish
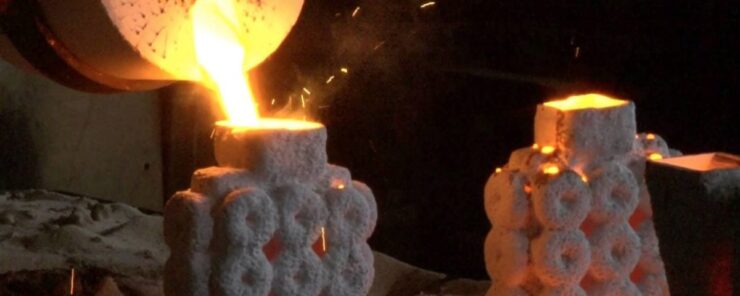
Improving the surface finish in investment casting is a multi-step process that depends on various factors. Factors such as the type of melted metal, material grade, melt temperature, and structures used to cast can all affect the surface finish of an investment casted product.
The poured melt must have a homogenous and even distribution of components for a good surface finish. Any misalignment or uneven distribution will result in an interruption in directional flow, which can create lumps or bumps along the surface of the product during cooling. Molten metal should also be free from dross, oxides or any other contaminants that might interfere with cooling rate and produce undesirable surfaces.
Machine settings must be carefully calibrated throughout the entire casting process to maintain desired results. Carefully selected machine settings are used to control fill rate, withdrawal speed and porosity rate of the molten metal to create an uninterrupted solidification pattern within the cavities when cooled. Different parameters such as pouring time, mold temperatures and alloy composition should be closely monitored to ensure ideal surface conditions were achieved after solidified parts were released from its molds.
Investment castings also require careful management of post-machining processes such as grinding or shot blasting operations which influence final surface finish quality. These processes must be closely monitored on-site by highly trained technicians skilled in both investing casting procedures and other post-processing operations for optimal results. Attention must be paid to grinding times, abrasive hardness, velocities and loading factors for proper homogenization over desired surfaces before delivery to any end customer seeking ultimate satisfaction with high precision products created utilizing investment casting procedures today.
Steps to Improve Surface Finish
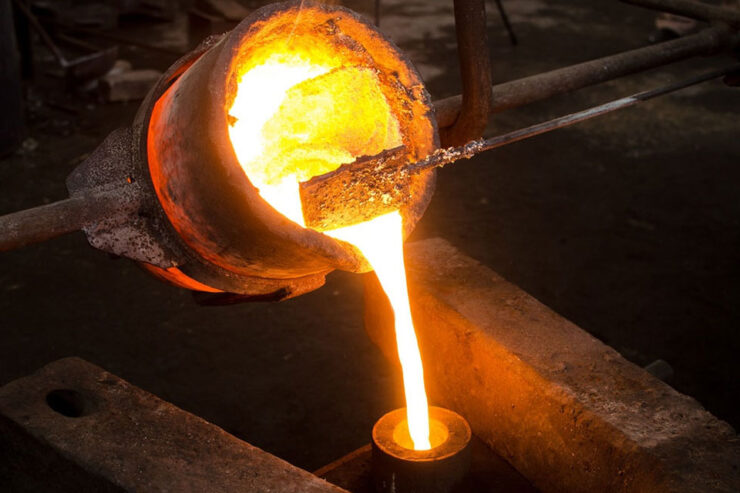
The casting process involves injecting liquid metal into a mold made from a wax pattern to produce an exact replica. There are several factors which play a role in achieving the best possible surface finish when using investment castings. The following steps should be taken in order to achieve the ideal surface finish:
- Adjusting the Wax Pattern: Adjusting the features of the wax pattern can have a huge impact on the final product. Finer details such as ratio and wall thickness can greatly affect surface finish, so it is important to pay close attention during the development and design stage of production.
- Maintaining Proper Temperatures: Proper control over temperatures during each phase of production helps to ensure that all materials are at the correct levels for proper material flow and flowability, as well as helping to prevent problems such as oxide build-up and shrinkage defects.
- Using Appropriate Pouring Temperatures: Different types of alloys require different pouring temperatures and mould preheat temperatures in order to produce ideal results. It is important to ensure that all alloys used are heated up appropriately before injecting into their molds in order to maintain their precise form and desired output throughout each step in production.
- Selecting Appropriate Coating Materials: When choosing appropriate coating materials for each part, certain criteria must be considered including porosity, adhesive strength, application method, viscosity and thermal properties of materials used which will help improve or guarantee surface finish or protect against oxidation or rusting across completed parts too.
- Optimizing Casting Parameters & Post Processing: Optimizing gating design when creating casting tools can help reduce solidification time drastically while maintaining consistent cooling rate through cavity walls; utilizing post processing correctly based on variables such as geometry complexity and requirements ensuring that surface finishes meet specifications can create truly accurate components every time.
Post-Casting Treatments
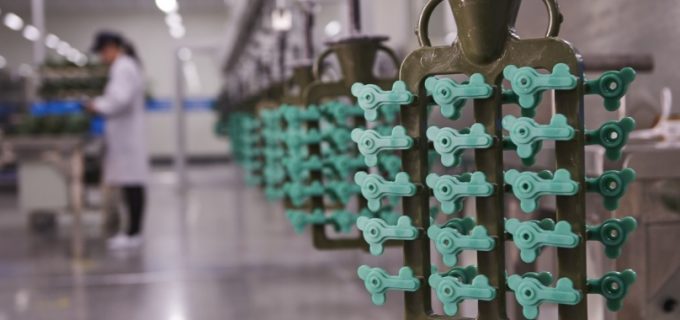
After a part has been cast, post-casting treatments may be required in order to improve its surface finish. Common treatments such as tumbling, grinding, and polishing may be used to help refine the surface of the part and remove any imperfections that may have occurred during the casting process.
Tumbling is a simple process where parts are placed in a rotating container with various materials (such as media or beads) designed to remove irregularities from the surface. The motion of the container causes these materials to abrade and polish the part’s surface at individual points around its perimeter. Tumbling is well suited for small parts that need minimal finishing and can easily achieve good surface uniformity.
Grinding is typically used when more detailed refinements are necessary. It involves manually running pieces over a grinding wheel in order to precisely polish them into shape, removing material as needed until you have reached your desired result. Similarly, polishing can be used to refine intricate details using cloths or additional chemicals applied directly to the part’s surface in order make it smoother than before. Both methods can help produce an optimal finish that one could hope for after investment casting.
Conclusion
It offers an opportunity to produce high quality components with excellent surface finish. By properly controlling the key factors of wax pattern design, shell building and metal pouring, the quality of the finished part can be significantly improved. To further enhance the surface finish and material properties, several post-casting treatments can be considered such as shot-blasting or polishing.
Furthermore, innovative alternative technologies such as slurry on sand cores or metallic 3D printed patterns offer promising potential to industry from both economical and environmental perspectives which will continue to develop with new materials and processes being introduced. Ultimately, to achieve the best results in terms of surface finish from investment casting requires individual optimization for each component design by considering all available options at each stage of the process.